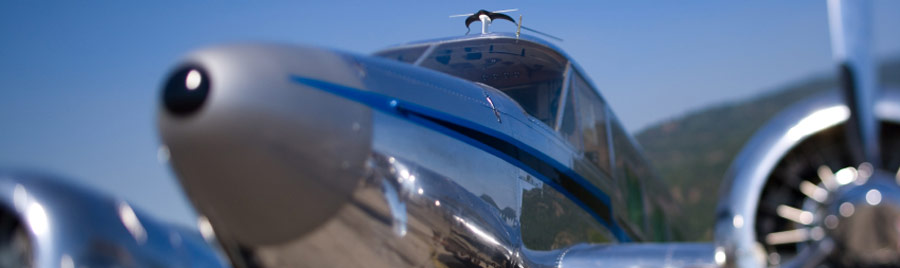
FLUID FILM® Exceeds Expectations & Requirements in Aviation and Aerospace
In the critical aerospace & aviation industries, corrosion preventives and lubricants can face a vast and extensive battery of tests to reach chemical approval. FLUID FILM® has faced intense scrutiny by government research laboratories as advanced as Boeing’s Space Systems Division for use on the Space Shuttle and Boeing’s Engineering Materials and Process Laboratory for use on aluminum alloys, exceeding process requirements and expectations, ultimately resulting in reduced maintenance costs.
FLUID FILM® has proven so effective in these industries that specifications were written by the U.S. Navy/Army/Marine Corps, Sundstrand Aerospace, Boeing North America, U.S. Coast Guard, U.S. National Guard, Sikorsky Helicopter and Delta airlines for the use of FLUID FILM® in a variety of applications.
The U.S. Air Force, in accordance with Mil-C-16173-E Grade 2, conducted testing on FLUID FILM®. FLUID FILM® exceeded all performance requirements.
All Applications Listed
- Aircraft Under-Wing Bolts & Nuts
- Bilge Area
- Cabin and Cockpit Seat Tracks
- Cable Pressure Seal Lubrication
- Cable Pulley Lubrication
- Cargo Door Tracks and Rollers
- Clean & Lubricate Cable Turn-Barrels
- Cowlings and Fairings
- Dry Bay
- Electrical Connections
- Flight Control Bell Crank Lubrication
- Free Up Adjusters & Lubricate Same in Flight Control Assemblies
- Fuel Bay Cells
- Gravity and Single Point Refuel Compartments
- Helicopter Outer Interior Bays with FLUID FILM & FLUID FILM Liquid A
- Hinges & Guide Pins
- Horizontal Stabilizer
- Hydraulic Fittings and Unions
- Landing Gear Doors
- Liquid AR for Stabilizer Vertical Rods
- Main Landing Gear Wheel Wells
- Nose Wheel Well
- Pylon
- Rudder and Elevator
- Turrets & Aircraft Carrier Elevator Guide Rails
- Upper Deck Flight Control Rods
Applications in the Aviation Industry
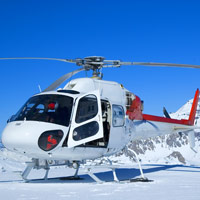
Aircraft & Helicopter
Interior door locking mechanisms and attachment hardware
Interior hatch locking mechanism and hardware
Jettison mechanisms and hardware
Locking tumblers
All hinges
All external jettison shafts and spring pins
Gas strut attachment points
Cargo door tracks and rollers
Battery terminal corrosion protection
Main door torque tube bearings
Areas requiring a light oil lubrication and corrosion protection
Freeing-up seized, rusted, corroded or otherwise frozen bearings, bushings, rollers and fasteners.
All door latches
Laboratory testing by Boeing Mesa for corrosion preventive measures on typical metallic substrates used in the helicopter industry found that FLUID FILM liquid A provided superior protection to all comparative tested products on Magnesium alloys, 4130-low carbon steel, 2024-T3 bare aluminum, AM-355 and 301 stainless steel, titanium, nickel and tungsten. – Engineering Report Materials and Processes Laboratory, Boeing Mesa, 1-15-98
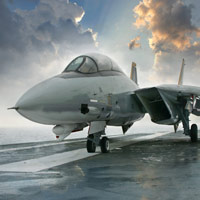
Magnesium Parts
FLUID FILM® proved so successful at protecting magnesium that Sundstrand Aerospace wrote specification number MS02-43-01 for FLUID FILM®, which is now used throughout the Helicopter Industry.
Laboratory and field testing of FLUID FILM® by the US Coast Guard for use on Sikorsky HH#F helicopters demonstrated maintenance cost reduction. FLUID FILM® subsequently incorporated into maintenance schedules for several aircraft types. ARSC Engineering specification GEN 200000.0113 – October 1993.
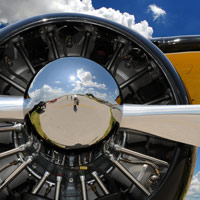
Flight Control Pushrods
Apply FLUID FILM® Liquid A on the inside of the tube and on the adapter/reducer tube external surfaces after adjustment in order to encapsulate the entire adjustable end. Apply FLUID FILM® Liquid AR on all internal and external threaded surfaces before assembly of the pushrod.
The Coast Guard Air Station Clearwater evaluated Fluid Film AR on the upper deck flight control rods and found it to be “extremely effective” for this application.